Definition of hot-dip-galvanising
Hot-dip galvanizing according to DIN EN ISO 1461, also known as batch galvanizing or discontinuous hot-dip galvanizing, is the application of a zinc coating to steel or cast parts by immersing the prefabricated and pretreated workpieces in molten zinc.
Conditions for a good result
The responsibility for good galvanizing quality does not only lie with the hot-dip galvanizing plant. The client must create the conditions for a good galvanizing result. The rules for hot-dip galvanizing design and production and other aspects must be observed, which are mainly described in Chapters B, C and D of the hot-dip galvanizing worksheets.
Procedural steps
Following the necessary steps ensures a good end result
The steps described below provide an example of the hot-dip galvanizing process (Fig. 2). Deviations may occur depending on the respective operational conditions; this applies in particular to systems for galvanizing small parts.
Delivery and incoming inspection
After the parts to be galvanized have been delivered and the necessary incoming inspection has been carried out, the workpieces are first put together into batches of components that are as similar or similar as possible so that economical galvanizing is possible.
Pic 1: procedural steps of hot-dip-galvanising
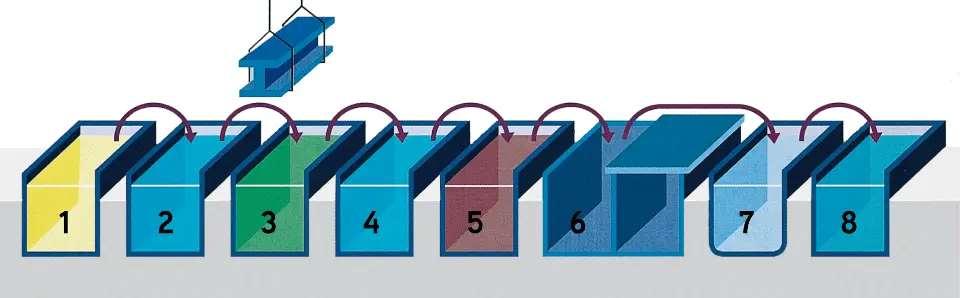
1 DEGREASING / 2 RINSING
Aqueous alkaline or acidic degreasing agents are usually used for degreasing. This is usually followed by a brief immersion in a water bath in order to prevent degreasing agents from being carried over into the galvanized material.
3 STAIN / 4 RINSING
Aqueous alkaline or acidic degreasing agents are usually used for degreasing. This is usually followed by a brief immersion in a water bath in order to prevent degreasing agents from being carried over into the galvanized material.
5 FLUXING / 6 DRYING
The rinsing bath is followed by a flux bath. The flux carries out a final, intensive fine cleaning of the steel surface and also increases the wetting ability between the steel surface and the molten zinc. Flux usually consists of an aqueous salt solution, usually zinc and ammonium chloride. Flux can also be applied in other ways, for example by spraying in liquid or powder form or by a foamed blanket of flux floating on the zinc bath. In most cases, fluxing is followed by drying, which dries the flux film using heat. In many hot-dip galvanizing plants, the waste heat from the galvanizing boiler is used to heat drying ovens and also degreasing baths.
7 Hot-dip-galvanising
After drying, the galvanized material is dipped into the liquid zinc melt. Zinc has a melting temperature of approximately 419 °C. The operating temperature of a galvanizing bath in most companies is between 440° and 460°C. In special cases, the zinc bath temperature can be more than 530 °C (high-temperature galvanizing). According to DIN EN ISO 1461, the zinc content of the melt is at least 98%. Zinc melts are usually alloyed with other metals to achieve an optimal galvanizing result. After the galvanized material has been immersed in the molten zinc, the parts remain in the zinc bath until they have reached its temperature. After the flux has been "boiled off", the surface of the zinc bath is cleaned of oxides and flux residues. The galvanized material is then pulled out of the zinc melt again (Fig. 3). During the galvanizing process, a coating of iron-zinc alloy layers of various compositions is formed as a result of the mutual diffusion of the liquid zinc with the iron in the steel. When the hot-dip galvanized objects are pulled out, a layer of zinc usually remains on the top alloy layer, the composition of which corresponds to the zinc melt.
8 Cooling and checking
The hot-dip galvanized steel parts cool either in air or in a water bath. In a final step, the finished galvanized material is then weighed, as the galvanized weight usually forms the basis for the company's price determination. The quality of the hot-dip galvanizing is checked before delivery. If necessary, the parts are then plastered, i.e. zinc peaks and residues on the zinc coating are removed if necessary.
Result
An important criterion for the quality of hot-dip galvanizing is the thickness of the zinc coating. It is measured in µm (l µm = l/l 000 mm), more rarely given as a mass per unit area in g/m². DIN EN ISO 1461 "Zinc coatings applied to steel by hot-dip galvanizing (piece galvanizing)" specifies the minimum values of the required coating thicknesses as they are to be provided for piece galvanizing depending on the material thickness (Fig. 4). If special requirements are placed on the appearance and thickness of zinc coatings, agreements must be made in advance between the client and the contractor.
Pic 2: Quality control of galvanised items.
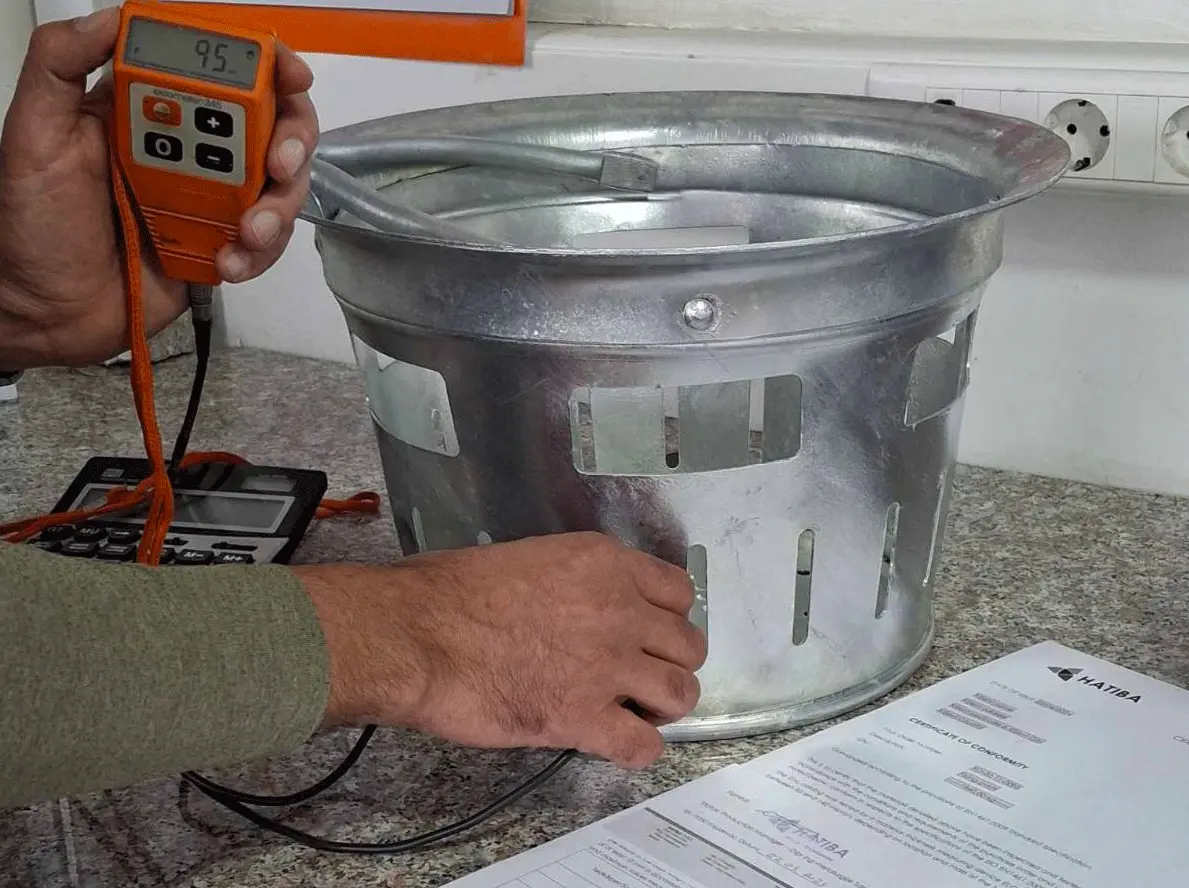